Maintenance management, asset value and the business world (1)
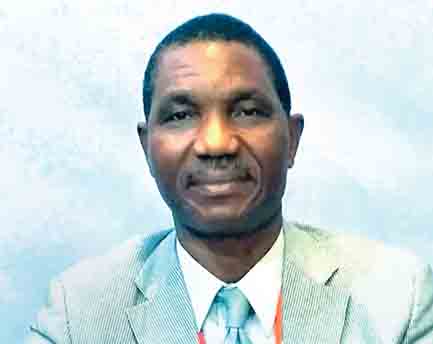
Olufemi Adedamola Oyedele, MPhil. in Construction Management, managing director/CEO, Fame Oyster & Co. Nigeria, is an expert in real estate investment, a registered estate surveyor and valuer, and an experienced construction project manager. He can be reached on +2348137564200 (text only) or femoyede@gmail.com
December 9, 2024527 views0 comments
According to the appraisal principle, maintenance is the livewire of assets (buildings, motor vehicles, plants and machinery). The value of most assets are affected by market forces (demand and supply), law on manufacturing and ownership of the asset, the role of the asset in the manufacturing of other assets, the process of manufacturing or of extraction of the asset, location to end-users, availability of alternative, usefulness of the asset and maintainability of the asset. Maintainability is the degree of the asset being able to be maintained (repaired, refurbished or replaced) and remain serviceable. While some maintenance departments rely on a run-to-failure (corrective) strategy, most of them want to do more preventive than corrective maintenance. The problem is that many organisations do not have the resources to expand their maintenance plan to include work that extends asset life and minimises downtime.
Organisations are now adopting a maintenance economy to elongate their assets’ life. A computerised maintenance management system (CMMS) can help organisations to extend their assets’ life. While it is certainly the job of the maintenance department to take on a break-and-fix role, there should be a balance between this break-and-fix (corrective maintenance) and preventive maintenance work. Key maintenance management objectives can reduce reliance on corrective maintenance and contribute to a more efficient and effective maintenance programme. Effective maintenance management can elongate the life of assets.
Objectives of maintenance management
The eight maintenance management functions and objectives are:
Read Also:
- Control costs and budget
The first objective of maintenance management is to control cost and budget. The maintenance manager budgets for maintenance and allocates the budget he is given to various areas of the department’s resources to ensure everything works effectively. It is important to include funds for both planned and emergency or corrective maintenance in the budget. The thing to keep in mind when budgeting for maintenance work is that when a major asset breaks down completely, most likely the asset will be replaced no matter the cost so that operation can continue. Of course, a decision must be made between repairing the asset, replacing it, or purchasing a different type of machine. Maintenance managers are desirous of staying within the maintenance budget. However, when something like this happens, it justifies a maintenance budget overrun. Maintenance managers must make cost-effective and wise decisions when choosing parts, vendors, and new or replacement machines. They also need to balance the costs and benefits of preventive versus corrective maintenance.
Labour resources are another area in which costs need to be monitored closely. When the budget allows, maintenance departments might outsource work to save time. In many cases, however, this is not feasible and corners get cut or tasks get delayed. When there is not enough time to complete all of the necessary corrective maintenance, there is no realistic way to implement a preventive maintenance programme on top of what the team is already doing. For many organisations, they can implement this type of programme only when they have the upfront resources and money available to invest in it. However, after they overcome that hurdle, the payback from this investment will come over time.
- Comply with regulations
There are different types of regulations to follow, which vary by industry. While organisations in the building industry follow National Building Codes, organisations in the power industry; oil and gas industry must follow National Electricity Regulatory Commission (NERC) and Federal Environmental Protection Agency (FEPA) regulations, in addition to Occupational Safety and Health Administration (OSHA) regulations. There are many safety regulations that must be followed by the food and beverage industry, such as those advised by the National Food and Drug Administration Commission (NAFDAC). Local, state, and federal regulation compliance standards must be considered by the production team at all times. To maintain adherence to these regulations, it is important to make small plans that lead to accomplishing bigger compliance goals.
Examples of these plans include:
- Making sure there are adequate safety guards in place on all machines
- Inspecting assets for damage
- Having a system in place to report damage to assets and parts
- Documenting and reporting all repairs and replacements
- Plan maintenance work
Strategic maintenance management includes scheduling maintenance jobs ahead of time. This is important because it efficiently distributes the appropriate time and labour resources to proactive, preventive maintenance tasks, helping maintenance departments reduce the frequency of major asset failures. Maintenance managers must have a clear understanding of the structure of the company in order to schedule work effectively. It will help determine the priority of various jobs.
For example, if a technician is working on installing new shelves in the stockroom and a pipe bursts in a bathroom, that is an emergency in which he may need to stop what he is doing and help to make that repair, unless another technician is available. There are other scenarios in which the job prioritisation is less obvious, but an experienced maintenance manager should help make those calls each day. The truck needs to be in service to make sure deliveries of that product are made on schedule. If just a few tasks are prioritised incorrectly, the schedule can be thrown off for weeks. Maintenance work must be organised in a way that achieves optimal outcomes.
- Ensure personnel safety
Another objective of maintenance management is ensuring the safety of all personnel, inside and outside of the maintenance department. This is done through regular inspections of boilers, compressors, material handling equipment, and other assets that could become dangerous if they malfunction. When maintenance is properly managed, safety increases for everyone in the organisation. Many machines can be dangerous when operating normally, but even more so when it malfunctions. Proper training on the function of every asset, critical safety dos and don’ts, and emergency situation protocols are essential.
To be continued next week.
- business a.m. commits to publishing a diversity of views, opinions and comments. It, therefore, welcomes your reaction to this and any of our articles via email: comment@businessamlive.com